Supply Chain Innovation As Your Supply Chain Solution
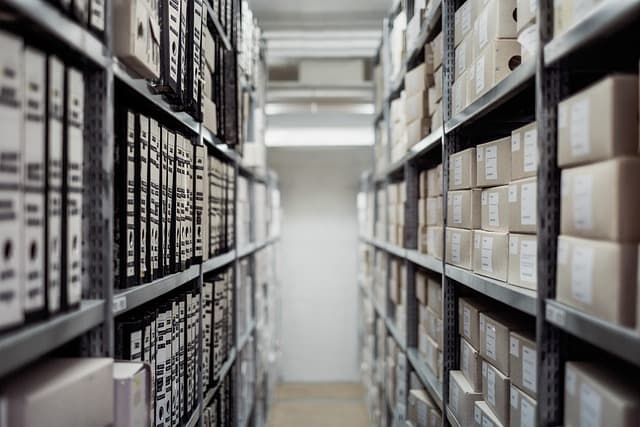
Supply chain innovation can make a difference in gaining or losing customers.
Supply chain operations are often behind-the-scenes activities but they have a big influence on an organization’s overall competitiveness.
To remain competitive companies are always striving to reduce defects in products and processes, reduce cycle times, reduce wait times, improve customer service, increase product availability, etc.
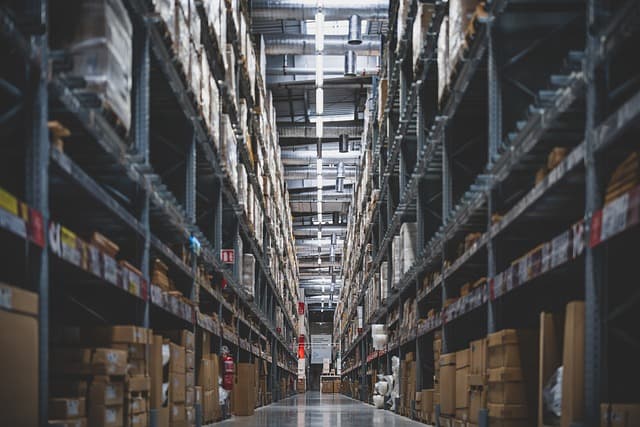
The global marketplace that we now operate in has further increased the competitive pressures that organizations face. As a result, it is more important than ever to take advantage of technological innovations, best practices, and process innovations, particularly with reference to improving your supply chain.
Supply chain innovation is about applying best practices and technological innovations to your own supply chain in order to reduce such cycle and wait times and other waste (to use a Lean term) in your in-house processes. This should have the ultimate goal of improving the customer experience. Give your customer more choice, more accuracy, faster order fulfilment, increased visibility, and better service by looking at areas in your supply chain where you can develop new practices / better ways of working.
BASELINE YOUR SUPPLY CHAIN PROCESS
In order to know that the best practices, new methods, and technological / process innovations that you apply have had a positive effect on your supply chain you first need to begin with a baseline of your current process.
Map out the “as is” process and use operational (including headcounts) and financial data (if applicable) to formulate a set of metrics related to your process. If you follow the Lean production practice in your organization then you might consider performing a value stream map of your supply chain process.
Document all the steps in the process map that you create and get domain experts for each stage in the process to comment on the effectiveness of each particular step.
Incorporating another Lean tool you might want to ask the “five why’s?” This is simply where you successively ask why a particular process step is done that way.
Try and focus on any waste in the process such as bottleneck and also closely analyze inputs and outputs, particularly with reference to outputs that act as inputs to the next stage in the process.
Time all the steps within the process and total these times to get a total start-to-finish time of the entire process.
BENCHMARK AGAINST INDUSTRY STANDARDS
Benchmarking gives you a chance to determine where you currently are with your process in relation to others.
Get your hands on published data where possible but also consider asking suppliers, customers, and other partners – they may have similar processes to yourself which you can benchmark against.
Obviously what is of utmost importance here is ensuring that you are in fact comparing like with like. There is no value in benchmarking against a process with many differences from your own.
It can be possible to benchmark processes with completely different non-competitive industries. Although your markets are different you might have similar supply chain processes.
DESIGN YOUR SUPPLY CHAIN INNOVATION
This is the part where you create your “to be” process map.
Here too it can be wise to contact non-competitive organizations, businesses that have no relation to your own may have best practices for a particular process that you are trying to enhance. For example to improve the interface with your end customer you might want to look at the hospitality industry’s best practices for interfacing with their hotel guests.
When designing try and use a modular approach that keeps interfaces and other linkages to a minimum. Complexity results in a difficulty to change further down the line. You want your design to be simple enough to be able to accommodate future products, future product changes, and any other beneficial changes.
Have your growth forecasts readily available and ensure that your design can cope with future demand. Scalability and flexibility are extremely important during the design of your supply chain innovation.
Be realistic about your design, and ensure all proposals are workable. To assist with the acceptance of the changes get the people who work with the process to be involved / part of the design. i.e. ask them for their advice, feedback, and ideas. People are much more likely to accept a process change if they feel that they were involved in the creation of the solution. For further information, please refer to the resistance to change article.
IMPLEMENT YOUR SUPPLY CHAIN INNOVATION
This is where you put all of your hard work into action. In an attempt to reduce risk try an agile-type phased approach if possible – making small well defined process changes that you can immediately test for success. Or alternatively, try piloting for just one product group or within one business unit before rolling the changes out to the wider group. This again can help in reducing the risk element and can also give you the ability to make some final tweaks and small improvements to your process prior to implementing on a wider scale.
Record metrics from your new process changes and use the metrics that you collected in the baseline and benchmark phases for comparison. There will be a lot of visibility on you in this stage of your supply chain innovation and therefore it is important that you get the buy-in from key stakeholders via demonstration of small positive quick wins/improvements (particularly to gain early confidence).
Once again it is important to refer to the earlier-mentioned change management article. You could have designed the most perfect process in the world but if you have every man and his dog against you it is never going to be implemented successfully.
CONTROL AND IMPROVE PHASE
Once you have implemented your supply chain innovation your job is still not complete. In order to ensure its continued effectiveness you should continue to measure and monitor the key metrics that you defined in your analysis.
To demonstrate that improvements are within or better than defined targets consider using statistical run charts. If possible look for ways to get this data automatically so that you can demonstrate effectiveness via real-time computerized dashboards.
You should also continue to look for further areas of improvement. Continuous improvement or kaizen to use the Japanese term is essential if you are to continue to stay ahead of your competitors.